To strengthen the melt blown fabric machinery, there are several steps that can be taken.
Here are a few possible suggestions:
Regular Maintenance: Regular maintenance of the machinery can help ensure that it is operating at peak performance. This can include cleaning, lubrication, and inspection of the components. A maintenance schedule should be created and followed to prevent breakdowns and increase the lifespan of the machinery.
Upgrade Components: Upgrading the components of the machinery can improve its performance and efficiency. For example, upgrading the heating elements, extrusion dies, and air compressors can improve the quality of the melt blown fabric and increase the production speed.
Optimize Process Parameters: The process parameters for producing melt blown fabric, such as temperature, air pressure, and melt flow rate, should be optimized to ensure consistent quality and efficient production. Regular monitoring of these parameters can help identify any issues and allow for adjustments to be made in real-time.
Train Operators: Proper training of operators can help prevent machine breakdowns and optimize production. Operators should be trained on the proper use of the machinery, as well as troubleshooting and problem-solving techniques. Ongoing training can help ensure that operators are up-to-date on the latest techniques and best practices.
Implement Quality Control Measures: Quality control measures, such as regular testing and inspection of the fabric, melt blown fabric machinery can help ensure that the fabric meets the required specifications. Implementing a comprehensive quality control program can help prevent defects and ensure customer satisfaction.
By implementing these steps, the melt blown fabric machinery can be strengthened, resulting in improved performance and increased efficiency.
Melt blown fabric machinery And Its Various Industrial Uses
Melt blown fabric machinery is a specialized equipment used in the production of melt blown nonwoven fabric, which is a type of material made from thermoplastic polymer fibers. This fabric is widely used in various industrial applications, including:
Filtration: Melt blown nonwoven fabric is commonly used in air and liquid filtration systems, such as face masks, air purifiers, and water filters. The fabric’s fine fibers create a tight weave that effectively filters out particles and contaminants.
Insulation: Melt blown nonwoven fabric is used as insulation material in various industries, including construction and automotive. The fabric’s insulating properties help to regulate temperature and provide sound insulation.
Wiping and cleaning: Melt blown nonwoven fabric is also used as a cleaning material in the form of wipes and cleaning cloths. The fabric’s absorbent properties make it effective in cleaning up spills and messes.
Packaging: Melt blown nonwoven fabric can be used as packaging material for delicate items, such as electronic components and medical equipment. The fabric’s soft texture and cushioning properties help to protect the items during shipping and handling.
Geotextiles: Melt blown nonwoven fabric is used in the construction industry as geotextiles for erosion control, soil stabilization, and drainage applications. The fabric’s permeable properties allow for water and air to pass through while retaining soil particles.
Overall, the melt blown fabric machinery plays a critical role in producing this versatile material, which has a wide range of industrial applications.
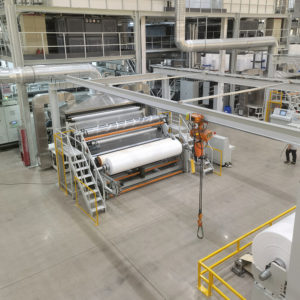