During the production process of wet wipes, several challenges or issues may arise that can affect the quality, efficiency, and reliability of the manufacturing process.
Some common challenges include:
Substrate Quality: The quality of the nonwoven fabric or substrate used in wet wipes can vary, and inconsistencies in substrate quality can lead to issues such as tearing, poor liquid absorption, or insufficient strength of the wipes.
Moisture Control: Achieving and maintaining the desired moisture level in wet wipes can be challenging. Inadequate moisture can result in dry or ineffective wipes, while excessive moisture can lead to leakage, mold growth, or reduced shelf life.
Solution Consistency: Ensuring consistent formulation and application of the wet wipe solution is crucial. Variations in the concentration or distribution of the solution can affect the effectiveness and performance of the wipes.
Folding and Cutting Accuracy: The folding and cutting process must be precise to achieve uniform sizes and shapes of wet wipes. Issues such as misalignment, improper folding, or inaccurate cutting can result in uneven or irregularly shaped wipes.
Packaging Integrity: Proper sealing and packaging are essential to maintain the freshness, moisture content, and hygiene of the wet wipes. Inadequate sealing or packaging defects can lead to drying out of the wipes, contamination, or loss of moisture.
Equipment Maintenance: Regular maintenance and upkeep of the wet wipes machinery are crucial for consistent production. Failure to perform routine maintenance can lead to unexpected downtime, reduced efficiency, or compromised quality.
Contamination Control: Maintaining a clean and controlled production environment is important to prevent contamination of the wet wipes by microorganisms, particles, or foreign substances. Contamination can compromise the safety and effectiveness of the wipes.
Regulatory Compliance: Wet wipes production must adhere to relevant regulatory standards and requirements, including those related to product safety, labeling, ingredient restrictions, and environmental considerations. Non-compliance with regulations can lead to legal issues and reputational damage.
Quality Assurance: Implementing robust quality control measures is essential to ensure that the produced wet wipes meet the desired standards in terms of performance, hygiene, and customer expectations. Quality control issues can result in customer complaints, product recalls, or loss of market reputation.
To address these challenges, manufacturers of wet wipes should implement quality control protocols, conduct regular testing and inspections, wet wipes machinery train operators on proper procedures, and invest in reliable machinery and equipment. Continuous improvement, feedback from customers, and staying updated with industry best practices can also help mitigate potential issues and enhance the overall production process of wet wipes.
What are some best practices for maintaining a clean and controlled production environment for wet wipes?
Maintaining a clean and controlled production environment is crucial for ensuring the quality, safety, and hygiene of wet wipes.
Here are some best practices to consider:
Good Manufacturing Practices (GMP): Implement and adhere to GMP guidelines specific to wet wipes production. GMP encompasses practices and procedures that ensure a high level of cleanliness, hygiene, and quality control throughout the production process.
Cleanliness and Sanitation: Establish and enforce strict cleaning and sanitation protocols for the production area. This includes regular cleaning of surfaces, equipment, tools, and storage areas using approved cleaning agents. Pay particular attention to areas that come into direct contact with the wet wipes.
Personal Hygiene: Emphasize the importance of personal hygiene among employees. Implement policies and provide training on proper handwashing, use of personal protective equipment (PPE), and adherence to hygiene practices such as wearing clean uniforms or protective clothing.
Contamination Prevention: Take measures to prevent cross-contamination. This includes implementing separate areas or zones for different stages of production, ensuring proper segregation of materials and equipment, and minimizing movement between clean and dirty areas.
Air Quality Control: Maintain good air quality within the production environment. Install adequate ventilation systems to control temperature, humidity, and air circulation. Consider air filtration systems to minimize the presence of airborne particles or contaminants.
Pest Control: Develop and implement a comprehensive pest control program to prevent pests from entering the production area. Regular inspections, sealing of entry points, proper waste management, and use of approved pest control methods are essential.
Raw Material Handling: Ensure that raw materials, including substrates and liquid solutions, are stored properly in a clean and controlled environment. Implement procedures to track and verify the quality and integrity of incoming materials.
Equipment Maintenance: Regularly maintain and clean the wet wipes machinery. Establish a preventive maintenance program to address routine servicing, calibration, and inspection of equipment to ensure optimal performance and minimize the risk of contamination.
Training and Awareness: Provide comprehensive training to employees on cleanliness, hygiene practices, and contamination prevention. Foster a culture of cleanliness and quality consciousness, where all employees understand their roles and responsibilities in maintaining a clean production environment.
Monitoring and Auditing: Implement regular monitoring and auditing procedures to assess the cleanliness and hygiene levels within the production area. Conduct inspections, environmental swabbing, and microbial testing to verify the effectiveness of cleaning protocols.
Documentation and Record Keeping: Maintain accurate and up-to-date records of cleaning schedules, maintenance activities, inspections, and audits. This documentation can help track compliance, identify areas for improvement, and demonstrate adherence to regulatory requirements.
By implementing these best practices, manufacturers can create and maintain a clean and controlled production environment for wet wipes. Regular evaluation, continuous improvement, and adherence to industry standards and regulations are essential to ensure the highest level of quality and safety in wet wipes production.
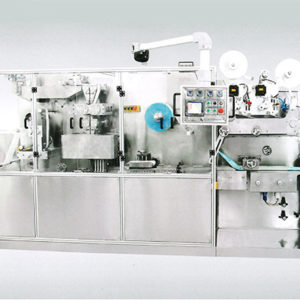